More than half the country’s auto suppliers are overwhelmed by the pace of the transformation to battery-powered vehicles, according to a study released this week by consultancy Roland Berger.
After spending decades perfecting the production of crankshafts, diesel injectors and other components not needed for electric motors, the industry is now scrambling to adapt as its traditional products become obsolete sooner than expected.
From global players like Robert Bosch and Continental to the hundreds of small- and medium-size companies, parts makers are key to Europe’s biggest economy.
Roughly 75% of the value-add of a car made in Germany comes from this supply network, which employs more than 300,000 people. Many of those jobs are dependent on how swiftly the sector can change.

Doing so will be a bit like merging onto a crowded autobahn at high speed. Suppliers started cutting personnel and pushing into electric-vehicle technologies before the pandemic hit.
The global health crisis hasn’t just devastated auto demand; it’s also led to a global chip shortage and fuelled material-price increases. In the midst of all this, carmakers and European regulators came out with more ambitious EV sales and emissions-cutting targets, hastening the demise of internal combustion engines.
“The ability to transform their product range is becoming an existential question for suppliers,” says Jan C. Maser, a partner at Roland Berger and one of the study’s co-authors.
“Companies have to invest heavily in new technologies — and that with stagnating production volumes and tight margins.”
Carmakers are exacerbating issues by producing more components in-house.
Tesla, VW and Porsche are making car batteries themselves or with a partner from outside the traditional car-parts industry.
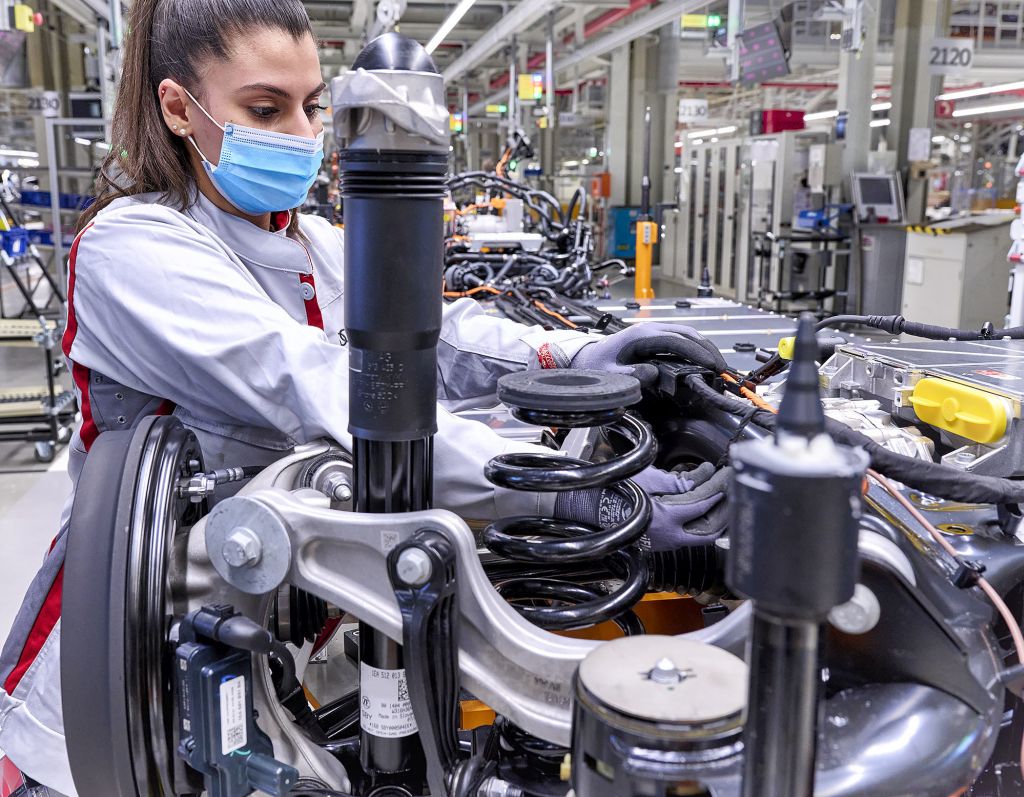
VW aims to cut procurement costs by 7% and fixed costs by 5% over the next couple years, potentially pressuring suppliers including Continental, Magna and ZF Friedrichshafen, my colleague Joel Levington wrote for Bloomberg Intelligence.
During a visit to Germany earlier this month, Tesla CEO Elon Musk publicly called out Bosch for not supplying chips quickly enough.
The industry’s struggles won’t be over soon. The semiconductor shortage will cut worldwide auto production by as many as 7.1 million vehicles this year, with pandemic-related supply disruptions hobbling output well into 2022, according to IHS Markit.
This week, VW's Wolfsburg plant — the world’s biggest, employing some 60,000 people — restarted from its usual summer break running only one shift.
Chancellor Angela Merkel’s government, which has been kind to the industry in past years, earlier this month green-lighted a 1 billion-euro “future” fund to help German regions reliant on autos survive the shift away from the combustion engine. Still, analysts anticipate greater consolidation of the parts industry.
So, what can suppliers do? Roland Berger says they must overhaul long-established processes to become leaner, invest more in software and digitization, become more open to R&D partnerships and look to Asia for potential growth.
Some have started the process. Hanover-based Continental, which abruptly replaced its CEO last year after falling returns and slow progress shifting to electric-vehicle components, is spinning off its powertrain unit Vitesco Technologies next month — albeit long after similar moves by rivals.

Germany’s auto suppliers are known to be great at solving problems. They’ll develop new products, raise efficiencies and carve out new niches. Still, the industry’s glory days are probably over: While a combustion drivetrain contains roughly 1,500 individual parts, an electric one has only 250. That’s a lot fewer slices of pie from which to feast.
Almost a decade ago, the potential for defective Takata air bags to explode in a crash erupted into the auto industry’s most complex and far-reaching safety crisis.
Roughly 100 million were recalled worldwide. Although the issue has largely faded from the public eye, defective parts continue to put drivers at risk, Andrea Navarro and Ryan Beene write in Businessweek.
As of early July, more than 14 million airbags still hadn’t been fixed in the US alone.
Millions of car owners remain unaware that the propellant used in their cars’ air bag inflators could be degrading as a result of heat and humidity, posing potentially deadly risk to those sitting in driver and passenger seats.