It’s no different at other major carmakers like BMW, Volkswagen or Mercedes.
This extra activity has nothing to do with lowering stress levels or teambuilding. Instead, it is a standard step for new production models to measure the size of the luggage compartment and provide customers with key information.
Cargo volume in a car is not simply calculated, but determined through a manual procedure, explains Opel spokesman Michael Blumenstein. According to Blumenstein, the engineers use building blocks with a standard edge length of 5 by 10 by 20 centimetres, which each have a volume of one litre and are stacked in the trunk.
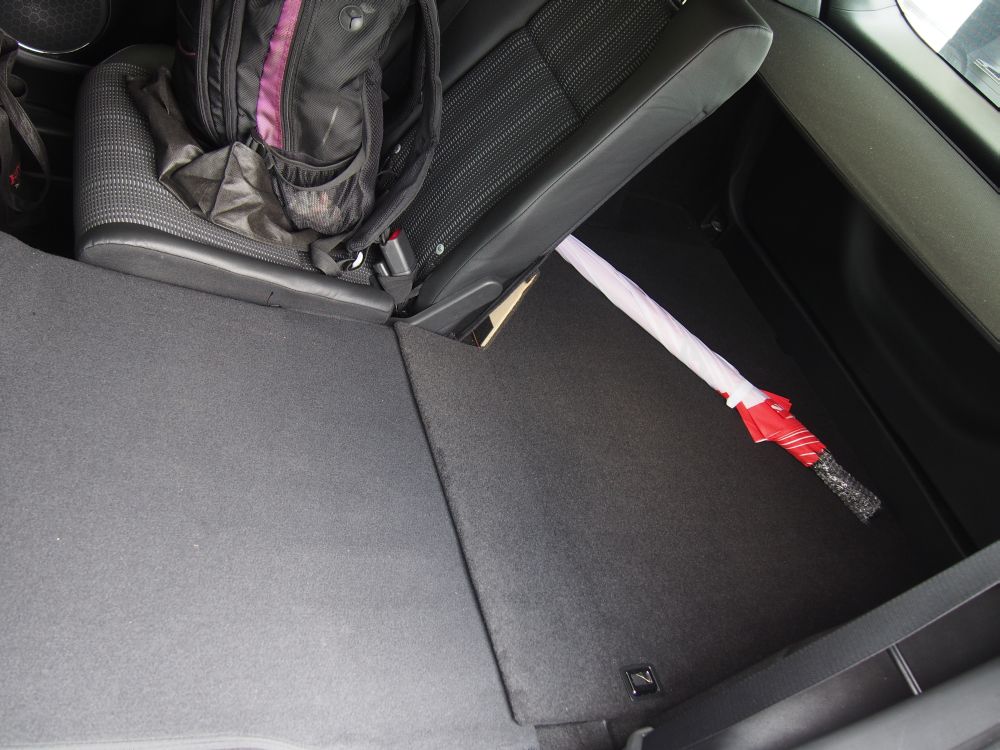
Some of the intermediate spaces, where you might be able to squeeze in a jacket, are left unused, Blumenstein admits. But this method does take into account the fact that suitcases and boxes are also not completely flexible and have sharp corners and edges.
However, as Christian Buhlmann of VW points out, engineers don’t necessarily end up playing with blocks or tetra-packs in automotive facilities around the world. In the United States, for example, volume and cargo capacity are simply calculated based on the units of measurement available and are therefore not actually comparable to European values.
Depending on the vehicle model and interior trim, the figures obtained in the United States, which tend to be in accordance with standards set out by the US-based Society of Automotive Engineers (SAE), are often 20 to 30 percent higher than European figures obtained using International Organisation for Standardisation (ISO) standards.
Regardless of whether they use SAE or ISO standards, or whether the manufacturer is European, American or Asian, designers are struggling to find extra space and are constantly trying to make as much room as possible for kith and kin in their vehicles.
Among other innovations, engineers are building in double loading floors, using the empty space between the spare tire and toolkit as a "basement," cutting secret compartments into footwells and creating new rear bench configurations.
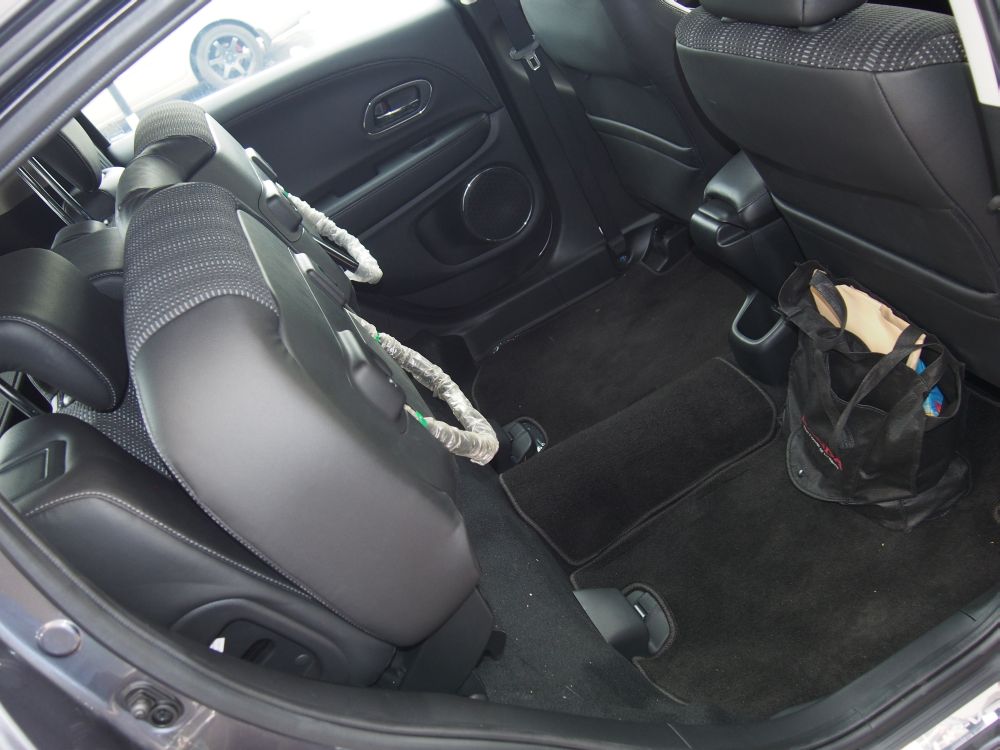
In the current Mercedes E-Class T-model, for example, there is a special cargo position for the rear seats, explains spokesman Steffen Schierholz.
With the help of a metal hook, the seat cushions are pulled and snapped into place at an angle 10 degrees steeper than normal. This, in turn, creates enough additional space in the trunk for 30 of the designers' one-litre blocks.
Similarly, rather than adjusting the angle of a seat back, a number of other vehicles, such as the VW Tiguan, have rear benches that can be shifted around, allowing either legroom or cargo space to be adjusted as desired.
"Flexibility is the key to family cars," says Hans-Georg Marmit from a major German safety inspection agency. "The more you can adapt a vehicle interior to your needs, the fewer compromises you have to make in your everyday life."
When it's possible to increase the length of the boot by folding back the passenger seat, you don’t need a 5-metre-long estate car just to occasionally transport a few long planks of wood.
Likewise, if the rear seats feature cinema-seat-style folding sections, like in the Honda Jazz or the Smart Forfour, you don't need a van with a high roof just to transport a large potted plant from time to time.