Nissan is producing prototype solid-state battery cells - which replace the electrical current-conducting liquid found in conventional batteries with a solid substance - at a facility resembling a pop-up lab inside its research grounds near its Yokohama headquarters.
The Japanese automaker plans to bring the new type of batteries to market by fiscal year 2028, readying a pilot plant for them ahead of that around 2024.
If they can be manufactured, solid-state batteries would unlock cheaper, safer and faster-charging EVs, according to automotive executives and battery experts.

Using different material combinations, Nissan predicts it will eventually be able to produce a solid-state battery pack that costs US$65 (RM275) per kilowatt-hour - a level at which analysts say EVs could reach price parity with gasoline-engine cars.
With its prototype facility, Nissan is joining almost every EV maker globally spending heavily on solving the slew of material and manufacturing issues that have thus far prevented solid-state batteries from making it into mass production.
Challenges with the batteries include a tendency to form spiky lithium structures called dendrites that can cause short-circuiting, and each manufacturer is working on its own solution.
With 10-plus years of research, development and major funding behind solid-state EV batteries, the fact that a few core technologies have not yet won out highlights the "very complex and difficult process of making a full solid-state battery that’s EV-sized and has quite a low rate of failure off the line,” said Max Reid, a battery raw materials research analyst at Wood Mackenzie.

Doi.
In line with Nissan’s timeline, Wood Mackenzie sees solid-state batteries as a technology that’s still "closer to 2030 than 2025,” Reid said.
In its drive to develop next-generation cells, Nissan - similar to Japan’s other top automakers Toyota Motor Corp. and Honda Motor Co. - is taking a different approach than many of its western peers.
While a number of car companies including Volkswagen AG, Ford Motor Co. and BMW AG have handed off development of solid-state cells to startups in the likes of Solid Power Inc. and QuantumScape Corp., Japanese automakers are pushing to keep research and development largely in-house.
To design new types of batteries "you need to start with the desired performance of a car, from there setting requirements for batteries and finally materials,” said Nissan corporate vice president Kazuhiro Doi.
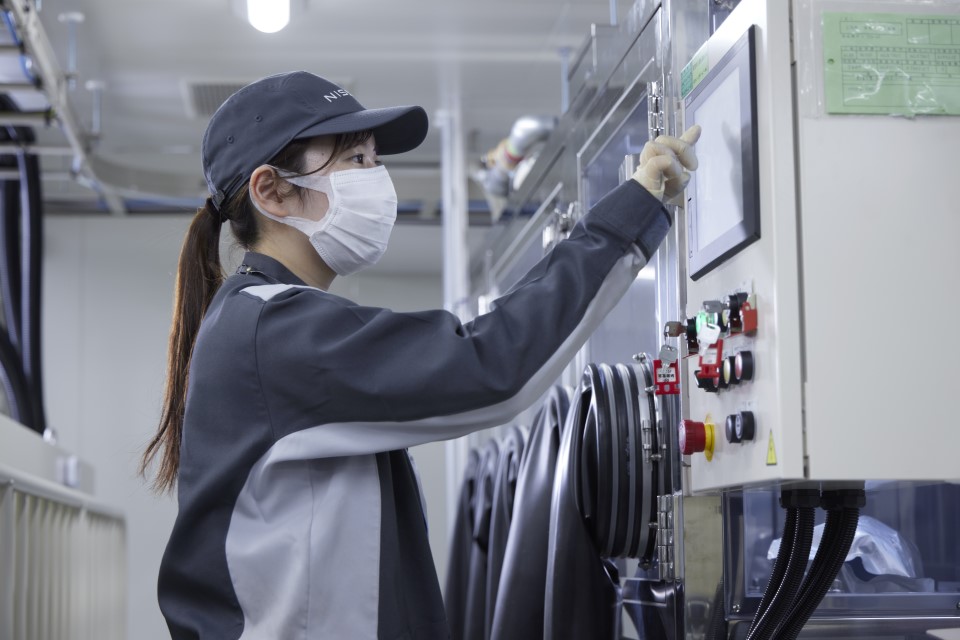
Creating that kind of battery-vehicle interplay is difficult for automakers specialising only in car design or battery makers focused solely on manufacturing cells.
That’s something Nissan learned while creating batteries for the world’s first mass-market EV, the LEAF, over a decade ago, according to Doi.
Nissan, though still in the "trial and error” period of development, has been able to design solid-state cells with roughly double the energy density of conventional liquid lithium-ion batteries, Doi said.
The company is working with some external partners, including Nasa, to use data and artificial intelligence to evaluate the countless potential combinations of solid-state battery materials.
At the current stage though, it’s difficult to gauge progress with regard to solid-state batteries given the secrecy of the battery industry, enforced by manufacturers seeking to protect their trademark technologies.
That opacity has led some developers to be accused of making exaggerated technical claims about their batteries.
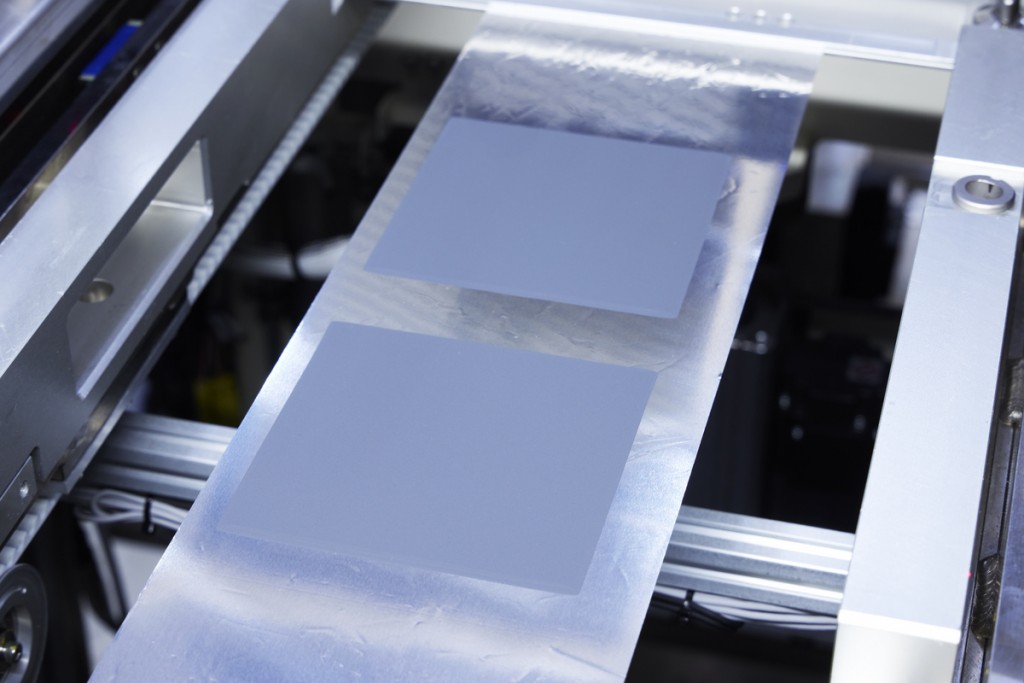
"To compare or measure companies’ success, we’d need to see them produce an EV pack worth of cells,” said Wood Mackenzie’s Reid.
"Whoever gets to that hurdle first would be one of the frontrunners.”
For now, Nissan’s Doi says that having internal R&D and production teams working on development gives the automaker a stronger sense of the battery’s commercialisation timeline.
"If we rely on others, we won’t have ample foresight,” he said.