After three years of research by the Bio-inspired Safety Systems (BISS) project, which had the German carmaker working alongside a consortium partners, it was found that the pomelo fruit is highly effective in impact protection.
The rind of the pomelo is also extremely light, much like an alligator's’ protective armour, which helps to distribute forces rather effectively.
The initial aim of the research project was to analyse the tissue formation, cell structure and function of these protection mechanisms and explore their suitability for use in industrially-manufactured products.
From there, the next step was to refine the corresponding fibre composites, layer structures and fibre orientation.
The project then went on to examine how functions that had previously been difficult to reconcile, like “crash protection”, “penetration resistance” and “damping”, could be combined in innovative protective systems using layering modelled on biological structures.
The results showed that it exceeded expectations with prototypes designed from natural models being up to 20% lighter, tougher and more stable than materials generally used today.
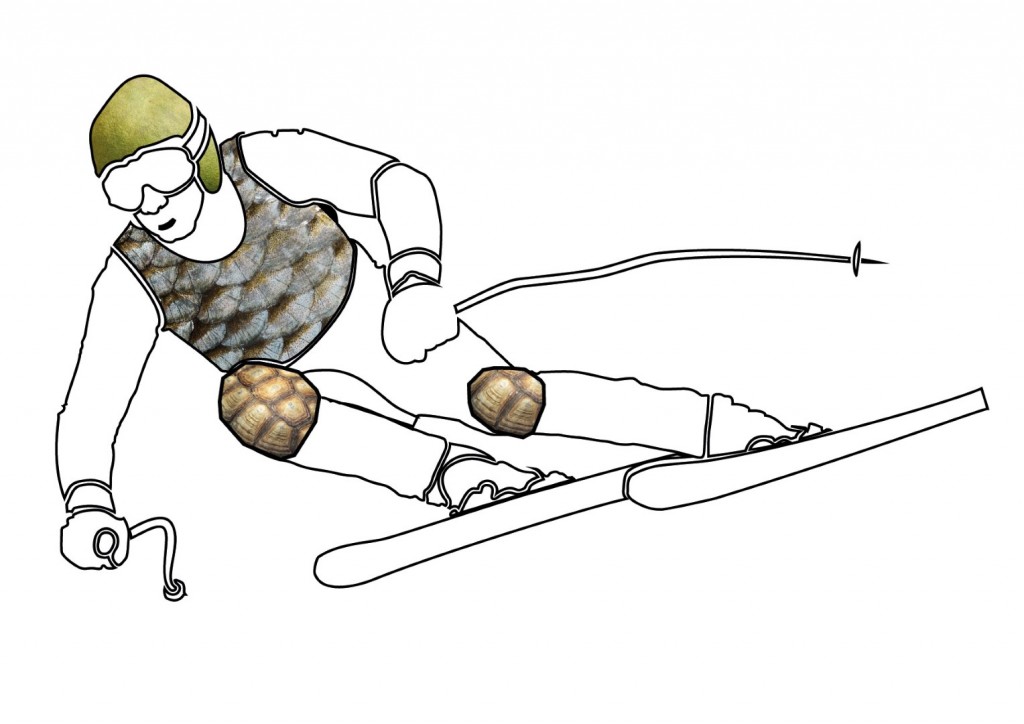
Impact protection: Scales of fish and many reptiles (alligator) overlap to create a composite system that stiffens under load to provide protection against injury. An Alligator's protective armour works in part by distributing force to neighbouring scales.
Also, the material can be produced economically and processed for the intended purposes.
The high level of functional efficiency achieved by biologically-inspired protective equipment also saves material. This not only makes both product and production more sustainable, but also less expensive.
Technology-forecasting experts at the BMW Group believe the most important learnings for the company lie in new approaches for enhanced employee protection.
Gloves and protective inserts made from bionic materials, for example, can protect workers on the assembly line from sharp-edged car-body parts.
The low weight, breathable design and flexibility of the research models mean that movement is barely restricted. Other potential applications include new forms of protective equipment for motorcyclists.
Research models of crash helmets and protectors offering the same level of protection weighed considerably less than conventional models available on the market.
The rind of the pomelo responds completely differently to pressure than conventional structures, which tends to give way and become thinner under the pressure point. Instead, the rind compresses and hardens faster.
A further characteristic of this atypical stress/strain behaviour is that the material actually becomes thicker when stretched, rather than thinner.
Within BISS, researchers have now managed to decipher the unique structure for natural protection and help produce composite textiles with a protective effect not previously achieved.
The results show that conversion of the foam network from ordinary to auxetic structures has a positive effect on the materials’ cushioning properties.
The stresses occurring during compression of auxetic polyurethane in the material are distributed optimally into previously unused, surrounding areas using the auxetic effect.
In this way, a larger volume of the material is involved in the energy absorption compared to ordinary polyurethane foams.
The BMW Group worked alongside adidas, ORTEMA, phoenix and uvex, as well as the Institute of Textile Technology and Process Engineering Denkendorf, Germany, the Department of Polymer Engineering at the University of Bayreuth and the Plant Biomechanics Group of the University of Freiburg, with additional support from partners such as the company Innovationsmanufaktur in Munich.
Also, the German Federal Ministry for Education and Research subsidised the project as part of its “Technical Textiles for Innovative Applications and Products – NanoMatTextil” programme.