It enables fast and efficient production of new prototype components right at the circuit. These can then be tested on the BMW S 1000 RR before they go into final production in Munich or at supplier locations. It also means that smaller parts that are often not subject to intense stresses can be made on-site and then used in races.
BMW Motorrad Motorsport brings along a portable 3D printer that travels to each circuit and is then assembled in the BMW Motorrad WorldSBK Team pit area on race weekends.
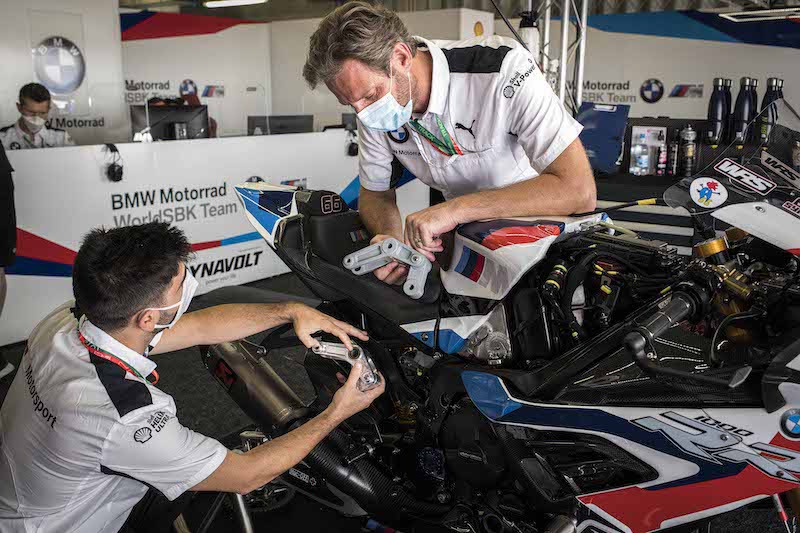
“This technology allows us to make improvements to the RR quickly and efficiently. The development of a WorldSBK bike is an ongoing process and it is often the minor details that make a motorbike better,” said BMW Motorrad Motorsport director Marc Bongers.
The on-site printer is backed up by the BMW Group’s in-house Additive Manufacturing Campus if more resources are required.
This channel provides the team with unique access to not only the advisory 3D printing experts, but also to a full range of printing methods and various materials for different applications. Manufacturing of the components can be triggered directly from the track, via BMW’s own systems.
Examples of parts that are printed in plastics or metals directly for use on the World Superbike include brake ventilation in plastics reinforced with carbon fibre, complex moulded parts, titanium crash pads, aluminium distributor boxes and aerodynamic trim parts.
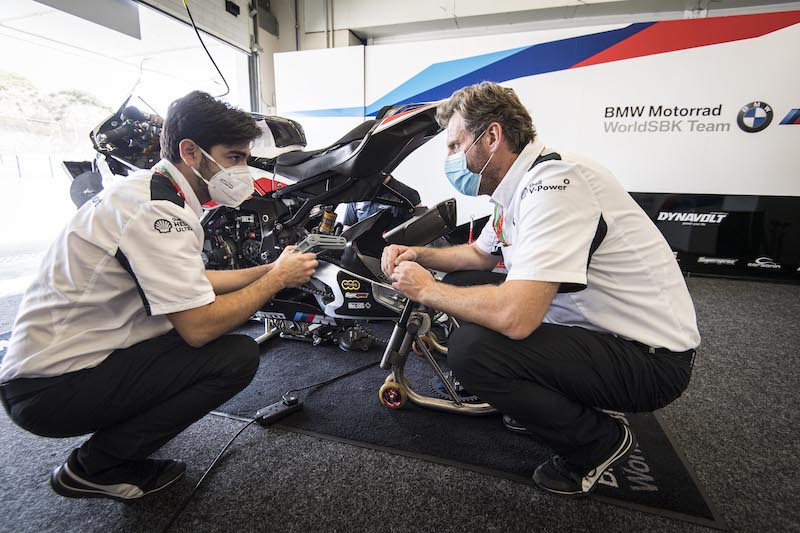