MELBOURNE: Other than supercar maker Koenigsegg, Ford and Australia-based Carbon Revolution has crafted the first mass-produced, track capable carbon fibre wheels for the venerable Shelby GT350R Mustang.
All 37 GT350R Mustangs will be the first mass-produced car to receive mass-produced carbon fibre wheels as standard fitment and weighing just a little over 8kg a piece.
Ford had set high testing requirements for the wheels, which needed to survive high-speed curb strikes, damage from ultra-violet rays and chemical exposure, and above all else - extreme heat durability up to 900-degrees C.
To combat these heat levels, the wheels feature a multi-material coating formulation to provide a thermal barrier.
A plasma arc gun was used to liquefy a ceramic material and the wheels were then coated at critical points around the inner hub and on the back of the spokes.
The result is an incredibly thin, nearly diamond-hard coating that shields the wheel from the GT350R’s 900-degrees Celsius potential for producing rotor heat.
The only drawback is that the flawless finish is a gloss black that hides the carbon fibre weaves.
In the curb-strike test, Ford said that due to the wheel’s lightweight, advanced construction methods and resins in the wheels, along with the highly-developed MagneRide dampers, the suspension was able to react so fast that the driver wasn’t sure the test had been carried out correctly and was thus required to repeat it.
The wheels also provide a reduction in rotational inertia of more than 40%, which positively impacts acceleration and braking performance.
A reduction in un-sprung weight (components not supported by the suspension) can have a significant impact on handling and performance by helping vehicles start, stop and turn faster by reducing wheel rotational inertia, dramatically improving response time to driver input.
In addition, lower un-sprung weight also translates to suspension components not having to work so hard to keep the tires in contact with the road over undulating or broken surfaces.
Ford said that the wheels are so light that the springs and MagneRide dampers had to be recalibrated because the suspension can respond considerably faster to road inputs.
Each wheel has a RFID chip with a unique tracking number embedded into the wheel’s structure, and each is individually entered into a quality assurance system.
Once this structure is assembled, it’s infused with resin and cured at high temperatures.
While the wheel cures, 61 individual checks and more than 246,000 data points are logged before being released from the machine.
To guarantee quality parts, the cured wheels are analysed using a 3D computerized topography (CT) imaging process in which more than 18,000 X-ray images are taken.
If the wheel passes inspection, it will undergo machining for the valve stem and mounting hardware holes before it gets painted, coated, assembled, dimensionally checked and shipped to Flat Rock Assembly Plant for installation on a new GT350R.
“The carbon fibre wheels reduce vehicle weight by 60 pounds (27kg) compared to aluminium, yet are stiffer for better steering response, we believe this is a game changer for the industry and a great example of improved performance through innovation,” said Ford Performance chassis supervisor Adam Wirth.
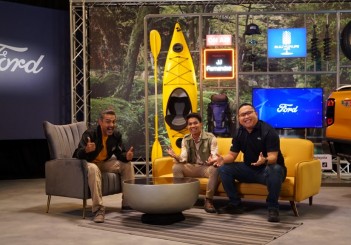