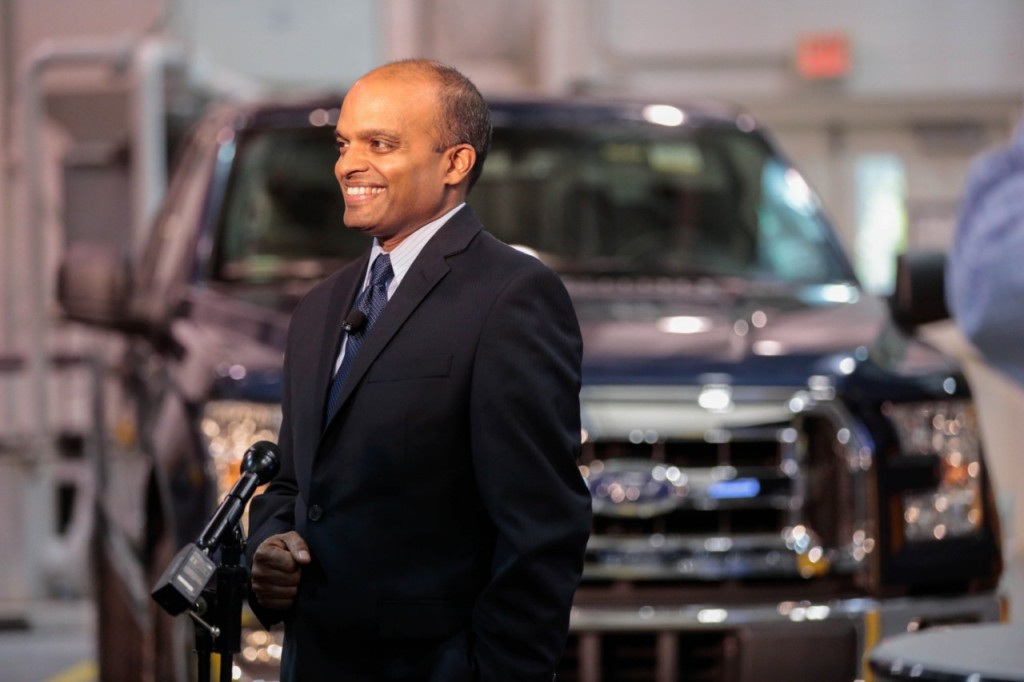
Raj Nair with the F-150 in the background.
DETROIT: Ford and Alcoa are working together to produce next-generation automotive aluminum alloys that are more formable and design-friendly.
Ford will use Alcoa’s Micromill material in multiple components on the 2016 F-150 – becoming the first automaker to use the advanced automotive aluminum commercially. The companies entered into a joint development agreement to collaborate on next-generation aluminum alloys for automotive parts using Micromill technology.
‘‘Light-weighting enables us to design vehicles with great customer attributes – like the F-150, which can tow more, haul more, accelerate quicker and stop faster than the previous F-150, and is more fuel-efficient than ever,” said Raj Nair, Ford group vice president and chief technical officer, Global Product Development. “This collaboration supports our continued drive for innovation, as we research automotive applications for even greater light-weighting.”
Alcoa’s Micromill technology, announced in December 2014, produces an aluminum alloy that is 40 percent more formable than today’s automotive aluminum.
“Alcoa’s breakthrough Micromill technology offers highly differentiated automotive material with strength, weight, formability and surface quality combinations previously impossible,” said Klaus Kleinfeld, Alcoa chairman and chief executive officer. “This high-tech aluminum will give Ford a true material edge enabling greater design flexibility and better vehicle performance – making the concept cars of tomorrow a reality.”
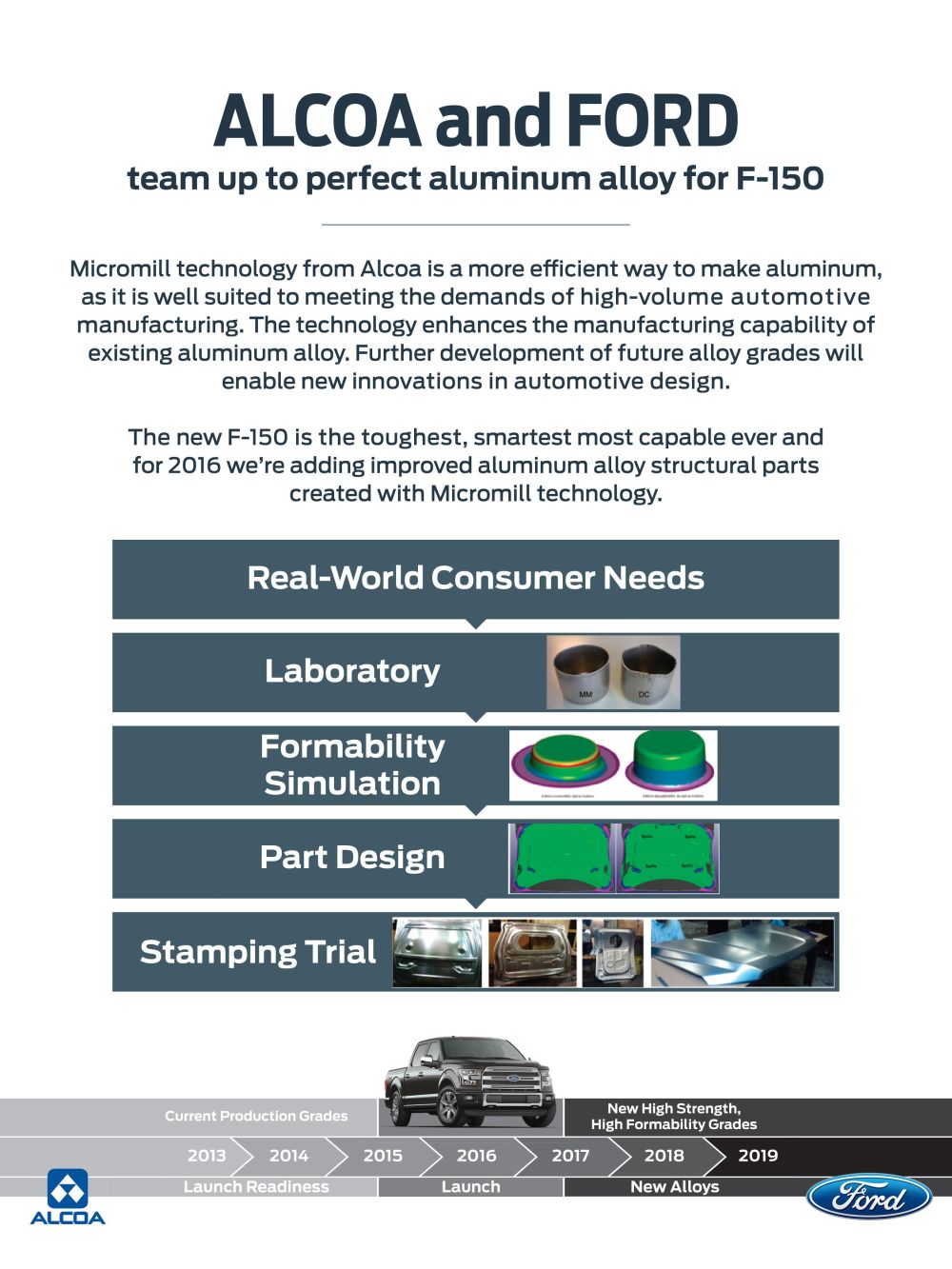
Micromill is the fastest, most productive aluminum casting and rolling system in the world combining multiple technologies into a streamlined production system. A traditional rolling mill takes around 20 days to turn molten metal into coil; Micromill does it in just 20 minutes.
Ford will begin using Micromill material in 2016 F-150 production in the fourth quarter of 2015, and plans to increase its use over the next several years on a range of vehicle components and future platforms. It is projected Ford’s use of Micromill material on its vehicles will more than double from 2016 to 2017.
Aluminum alloy produced using the Micromill process has already been validated by Ford engineers to ensure it meets the stringent requirements for producing high-quality parts, especially the kinds of complex structures that make up F-150.
Over in Europe, Ford is leading a €3.5 million research project to investigate the use of alternative fuels that could offer customers the power and performance of modern internal combustion engines with environmental benefits comparable to an electric vehicle.
The German government is co-funding the three-year project that will test the first-ever cars to run on dimethyl ether (DME), commonly used as a non-toxic propellant in aerosol spray gas, and oxymethylene ether (OME1), a liquid usually used as a solvent in the chemical industry.
Both ethers, which will power cars based on the Ford Mondeo, offer the potential for extremely low particulate emissions and enhanced fuel efficiency. They can be generated from fossil natural gas or bio-gas or through a sophisticated process called power-to-liquid that uses renewable sources such as solar or wind power together with CO2 captured from the air.
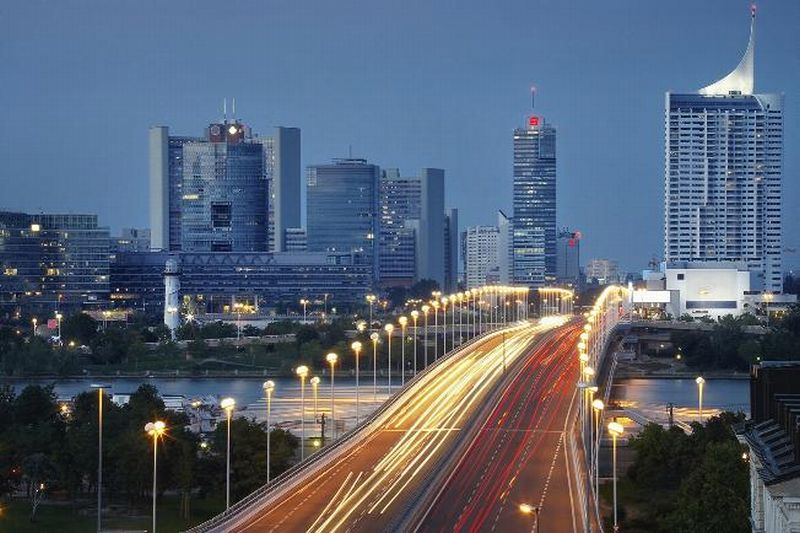
This promising technology is being investigated in a parallel project together with RWTH Aachen University researching the viability of different DME generation methods, looking at conversion efficiency, estimated fuel prices and infrastructure aspects.
“The CO2 produced by a car powered by DME from renewable sources could be comparable to the amount generated by a marathon runner covering the same distance – but with performance similar to a diesel powered vehicle,” said Werner Willems, technical specialist , Powertrain Combustion Systems, Ford of Europe. “This is a project that could help place vehicles with a significantly reduced carbon dioxide and particulate emissions on the market at affordable costs.”
Both DME and OME1 produce almost no particulates, and also share characteristics with diesel fuel that are expected to make conversion of diesel engines possible with comparable performance. It is estimated that DME from renewable energy sources could offer well-to-wheel emissions of about 3 g/km CO2. Like liquefied petroleum gas, DME must be stored in a slightly pressurised tank. OME1 can be stored in a conventional tank system. The DME-powered engines are expected to benefit from almost soot-free combustion, higher thermal efficiency and excellent cold start properties.
For the project Ford European Research & Innovation Center, Aachen, Germany, will work together with RWTH Aachen University, the Technical University of Munich, FVV, TUEV, DENSO, IAV Automotive Engineering, and Oberon Fuels. Through the FVV–the leading forum for joint research projects on engine technology in Germany – the project findings will be shared with key-players within the automotive industry.