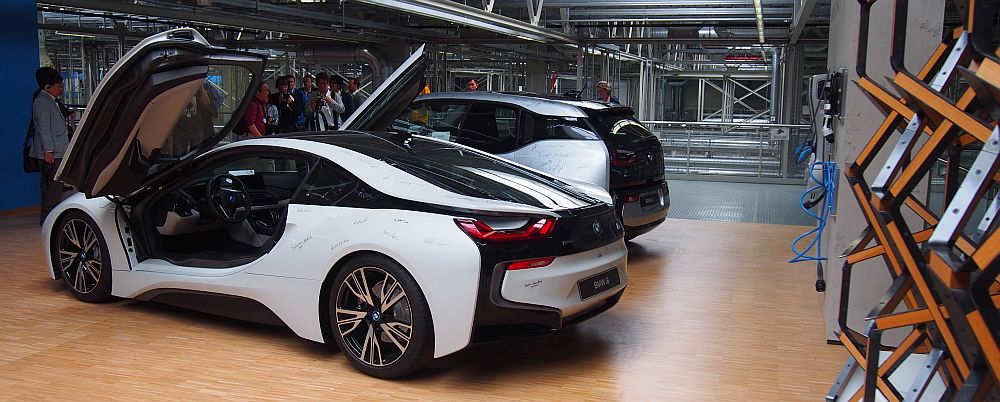
An i8 and i3 on display at the Leipzig plant.
What’s mostly reinforced plastic, powered by electric motor and held together by glue?
Say “i” and aye it is. We are referring to BMW’s i sub-brand, those cars that are its investment in a future that would bolster its relevance to a mobile public.
CarSifu has visited a number of car plants locally and abroad, and it’s always the same cookie-cutter processes that mark out those cars build for the masses.
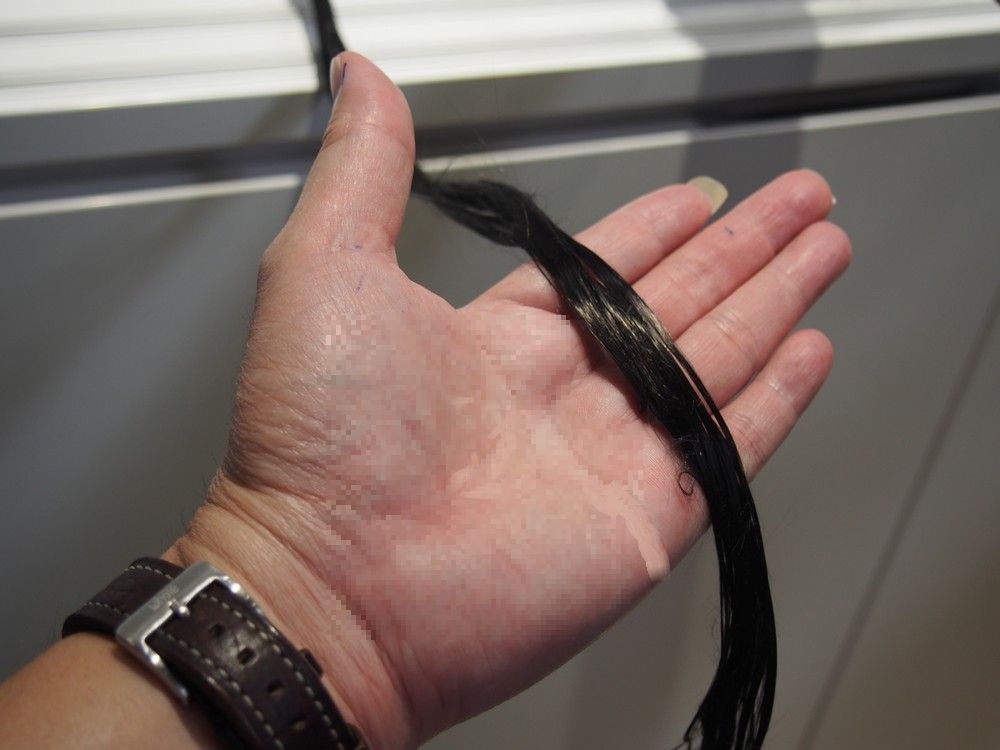
Carbon fibre strands.
Parts, sub-systems and chassis come together in an orchestrated process that’s precise to a fault. They are put together in stages either manually or by robots as they move from one section to the next, sealed against corrosion, spray painted and quality-checked before they are sent along to the stockyard.
Car manufacturing is a volume business and thousands of workers are typically employed. Such operations are also highly automated to speed things up as each car rolls off the factory floor, ready to be shipped to showrooms around the country and in many cases, around the world.
However, BMW’s Leipzig plant is not a run-of-the-mill factory. It’s one of the most modern, innovative and sustainable car factories in the world.
How many car makers can say they are able to mass-produce carbon fibre reinforced plastic (CFRP) parts? None, except BMW.
The Leipzig plant, sandwiched between BMW headquarters Munich in the south and Berlin up north, was opened in 2005 and is the hub where BMW makes its i cars since 2013. At 2.1 million sq m in area, it’s about the size of 300 soccer fields and employs 4,700 workers.
It produces the compact i3 urban EV and the i8, plug-in hybrid sports car. There’s spare capacity to build possibly a mid-range i5 electric sedan or plug-in hybrid. Other than the two i models, the Leipzig plant also produces the BMW 1 Series, 2 Series Coupe and 2 Series Active Tourer.
The i3 is already selling down south in Singapore although BMW Group Malaysia hasn’t announced plans to bring in the i3, as it waits for the government to make the first move. The i3 is also available with a range extender, a small petrol engine that doubles the car’s range to around 300km. The i8, however, is available locally at RM1.12mil.
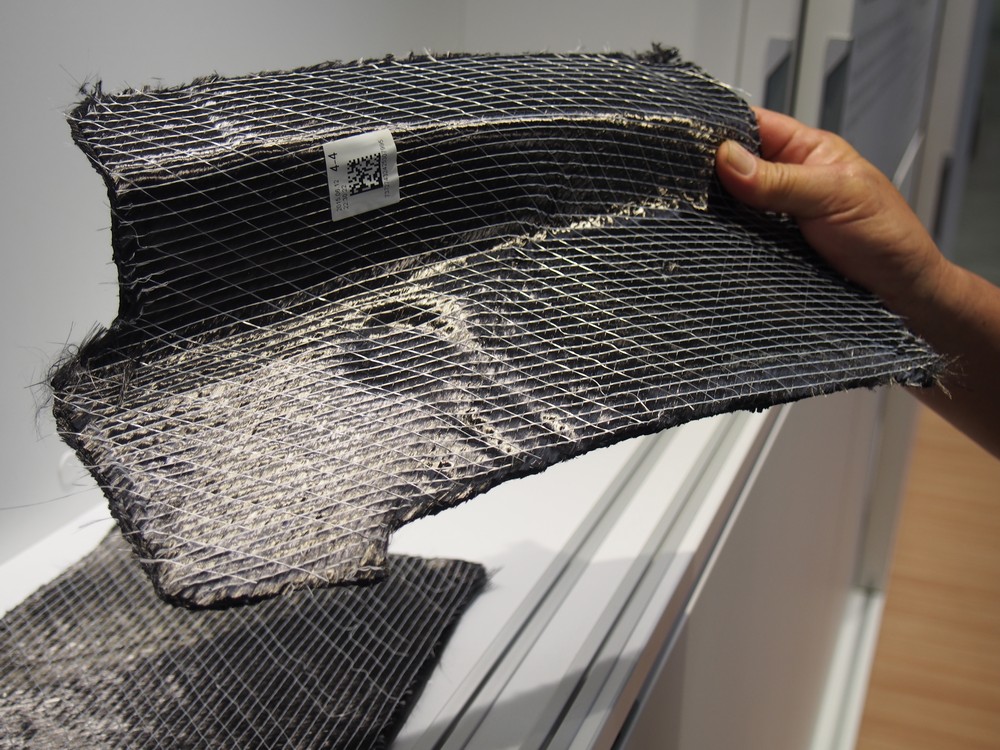
Moulded carbon fibre mat.
BMW plants across Germany are opened to the public. At the Leipzig site, visitors pay a small fee to go on a guided tour of the classic production (ie the 1 and 2 Series cars) or the i cars. Visitors are received at the central administrative building, an award-winning landmark created by British-Iraqi architect Zaha Hadid.
CarSifu visited the plant in June in conjunction with the preview of the new MINI Clubman in Berlin and a drive of the BMW X5 plug-in hybrid in Munich.
Prior to the i car tour in our case, we were briefed about the plant operations by its chief, Daniel Schaeffer.
He explained how the i cars were built, with parts coming from different factories across Germany. It sources its carbon fibre from a joint venture plant in Moses Lake, Seattle, in the United States.
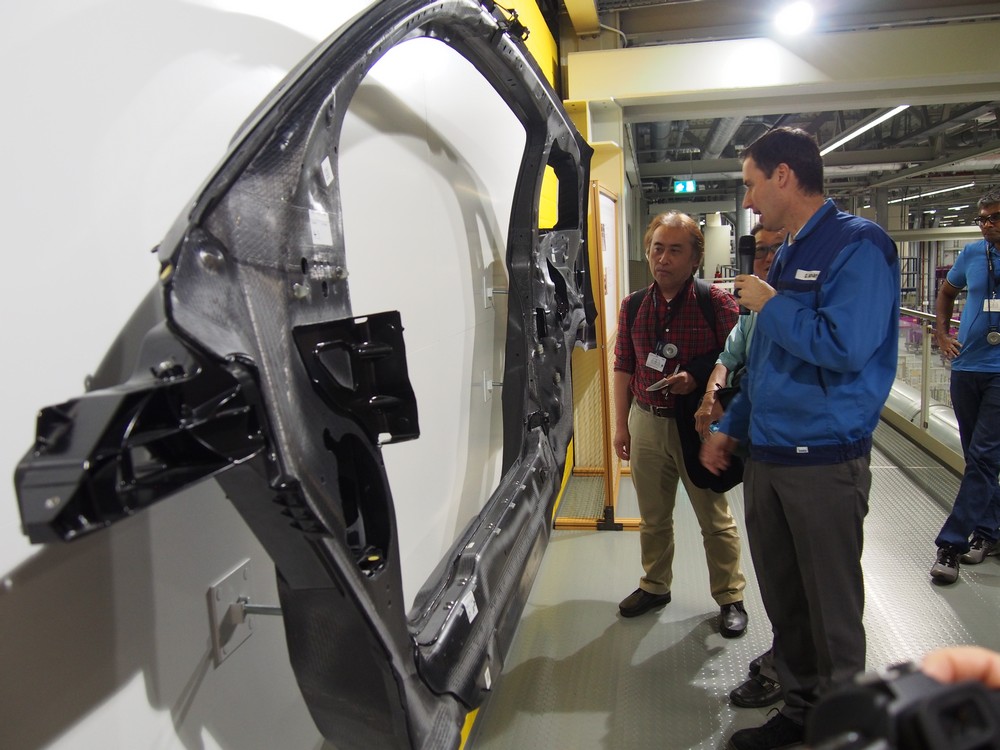
The CFRP side body of an i3 is unbelievably light.
Unlike making conventional cars, the i car production is simplified. i car production is unique in the sense that the metal stamping process for body components and painting stages are eliminated, resulting in a marked reduction in water and energy usage and thereby costs.
The i models are made of a Life module and a Drive module; the Life module being BMW-speak for the passenger cell made of CFRP parts, while the aluminium Drive Module is where the li-ion battery pack, powertrain, chassis and other structural features are found.
Exterior body panels, bonnet and bumpers/fenders are made with what BMW terms “unreinforced” thermoplastic.
Four buildings in the sprawling complex are dedicated to I production. With classroom briefing done, it was time for a walkaround. The body shop is linked to the assembly shop and the tour is conducted along a network of overhead walkways. Two other buildings a few blocks away make respectively the CFRP parts and exterior parts before they are transferred to the body shop and onwards to final assembly.
The visit ended with a look at how BMW makes composite panels.
BMW’s serial production of CFRP is an intriguing process and its technology is, some say, at least five years ahead of any potential rivals.
The CSL coupe was the first BMW to use CFRP on its roof 12 years ago followed by the M3 roof and M6 roof and bumper supports.
Unlike in the past where carbon fibre is woven in a time-consuming and costly manner, BMW's version is made of fibre bundles laid in the same direction per layer and sewn together
No autoclave is used. Instead, resin transfer molding (RTM) presses does the job of binding the mats to resins injected into the mold at high pressure to create the CFRP. The individual CFRP panels are then glued by robots to form the composite body shell or Life module.
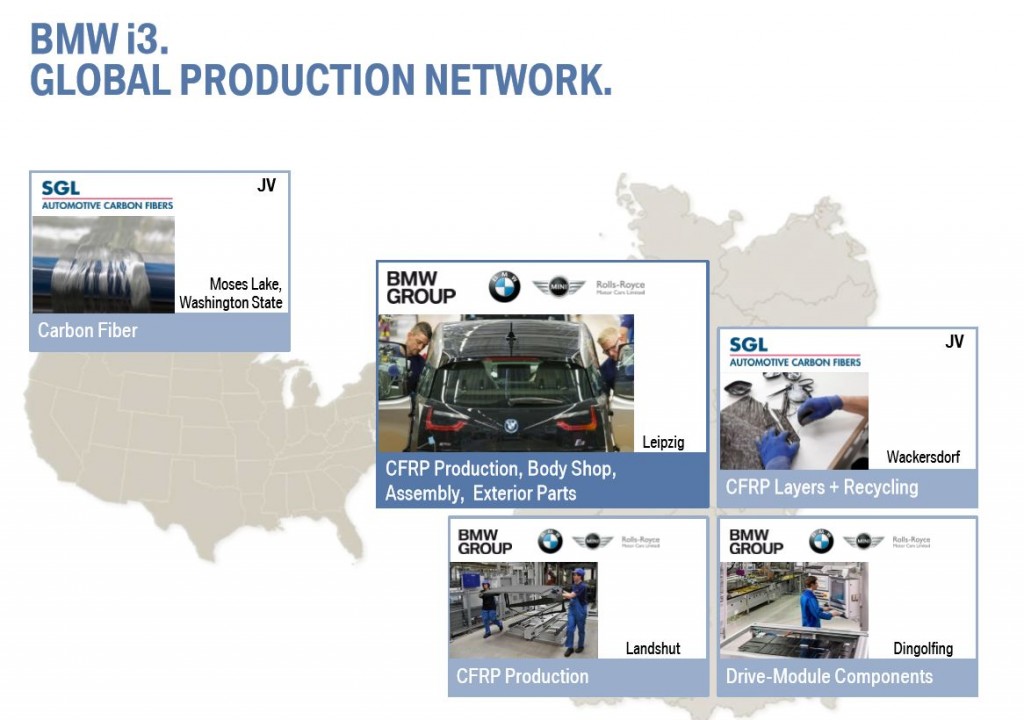
BMW has managed to shorten the production of composite panels down to merely 8 minutes compared to hours in the past. Excess mats do not go to waste as they are sent to another plant to be recycled.
Everyone knows carbon fibre reinforced plastic parts are light but just how light they are is eye-opening; you could lift an entire i3 side body panel with one hand. The lightweight Life Module of CFRP offsets the weight penalty of the Li-ion battery stack on the floor of the i3 and i8 and other components. BMW says CFRP weighs half as much as steel and 30% less than aluminium. And the other advantage is it doesn’t rust.
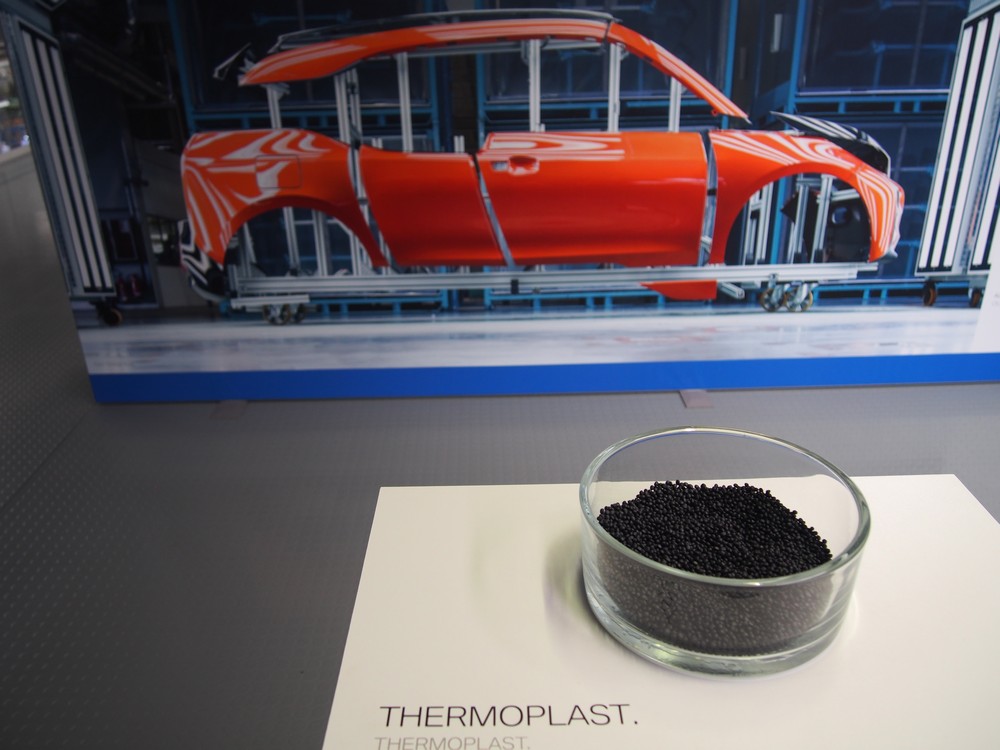
The Life Module is installed with interior fittings after it is mated to the Drive Module. The painted shell is then attached to the car body. At the end of the production lines BMW i Series and classic BMW models meet at the assembly finish.
Schaeffer also emphasised that BMW’s sustainability mantra is not just for public relations but manifested in the plant operations, with four turbines on site to provide all the energy needs for I car production. The turbines churned out an annual power production of around 26 GWh, which supplies 1/5 of the plant’s power needs. Sustainability is also seen in the use of natural fibres, recycled materials or renewable resources in the interior trim.
The Leipzig plant produces 740 cars daily, of which 100 are i3s and 20 are i8s.
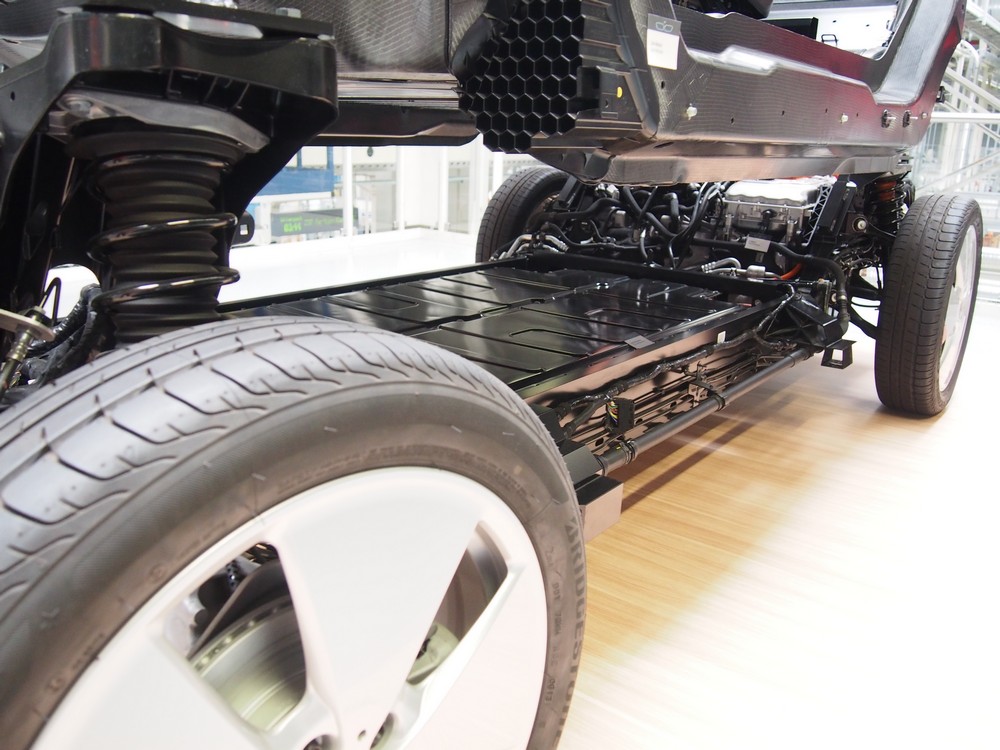
The lithium ion battery pack lies on the floor of the i3.
All that arcane knowledge gleaned from Project i is being shared with the core models, with the upcoming sixth-generation 7 Series featuring carbon fibre reinforcements in the passenger cell.
You can be sure the 7 Series won’t be the last to get the CFRP treatment.
Already there are murmurings that new patents BMW has filed could mean the expansion of CFRP use to its motorcycle chassis in future. We won’t be surprised if it comes to pass.
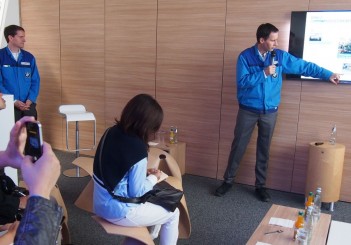
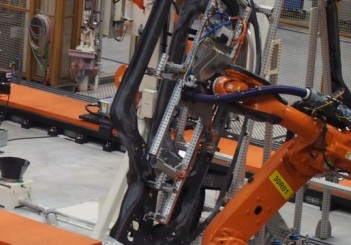
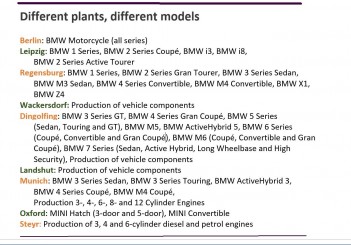
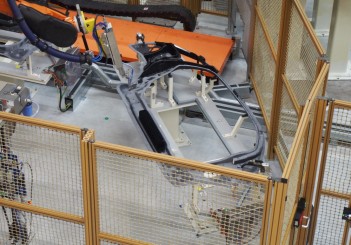
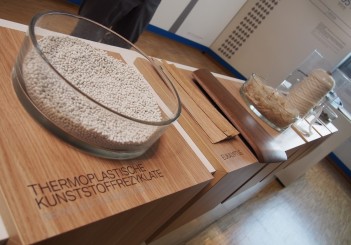
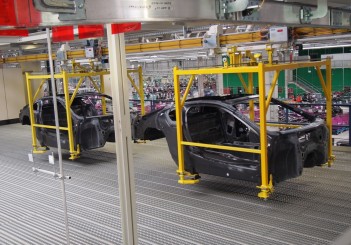
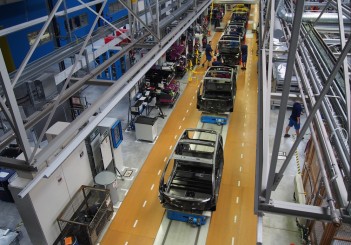
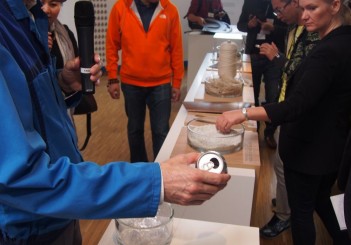
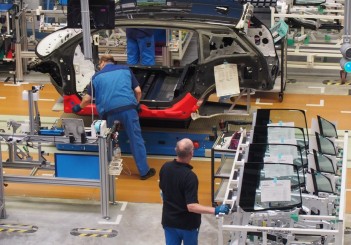
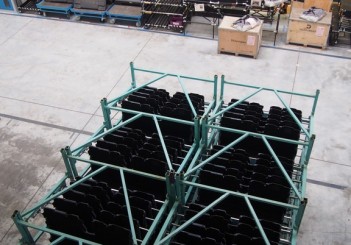
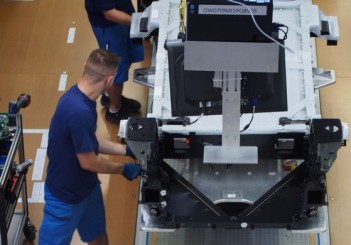
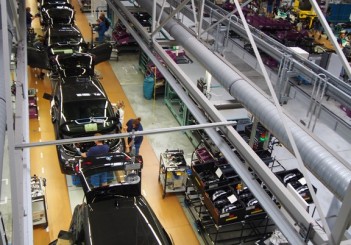
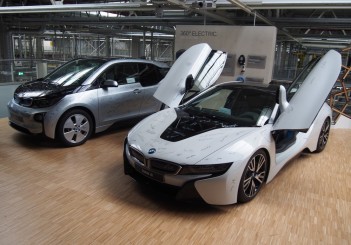
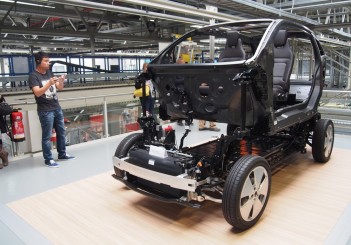
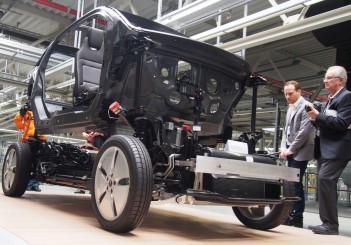
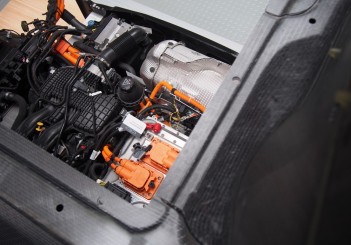
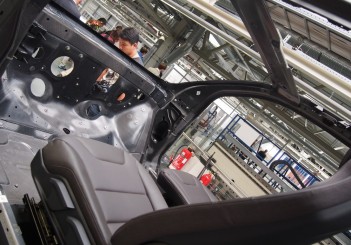
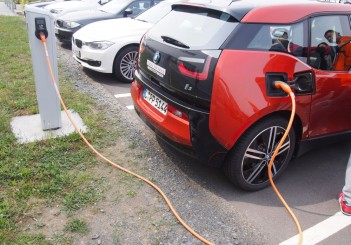
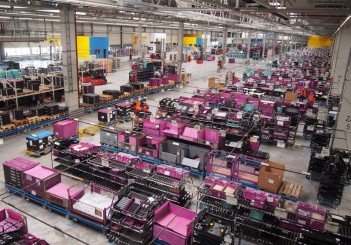
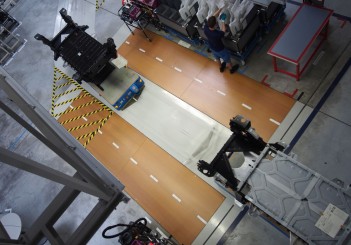