TANJUNG MALIM: Proton's locally-assembled 1.5 Turbo Gasoline Direct Injection (TGDI) engine is expected to be a feature in its future models that are derived from Geely platforms.
Designed to provide good fuel efficiency, smooth drivability and high specific power output, the 3-cylinder 1.5TGDI engine is capable of future development to reach the stricter Euro 6 emissions level.
The wider usage of the 1.5TGDI engine will also allow Proton to optimise on its investment in the new assembly line for the engine.
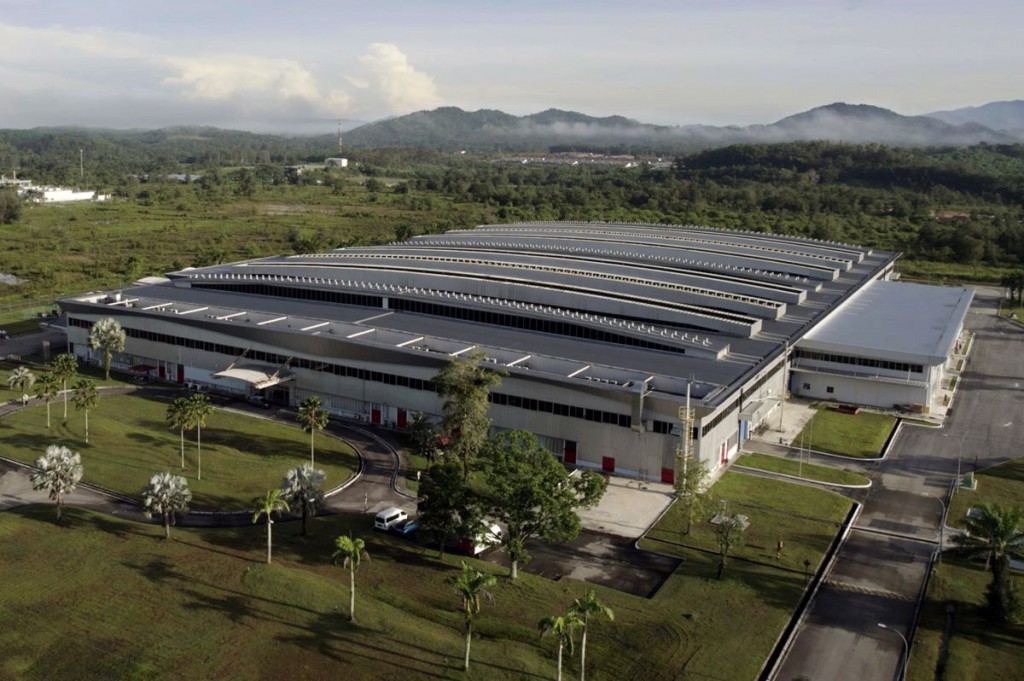
Proton Engine and Transmission Manufacturing building.
Among the traits of the 1.5TGDI that produces 177PS and 255Nm of torque are compact size, high tumble intake ports, variable valve timing, optimised thermal and lubrication systems, and a low inertia turbocharger.
The 1.5TGDI engine's development started in 2012 with the Volvo and Geely Engine Joint Development Programme at Volvo R&D centre and China Euro Vehicle Technology Gothenberg.
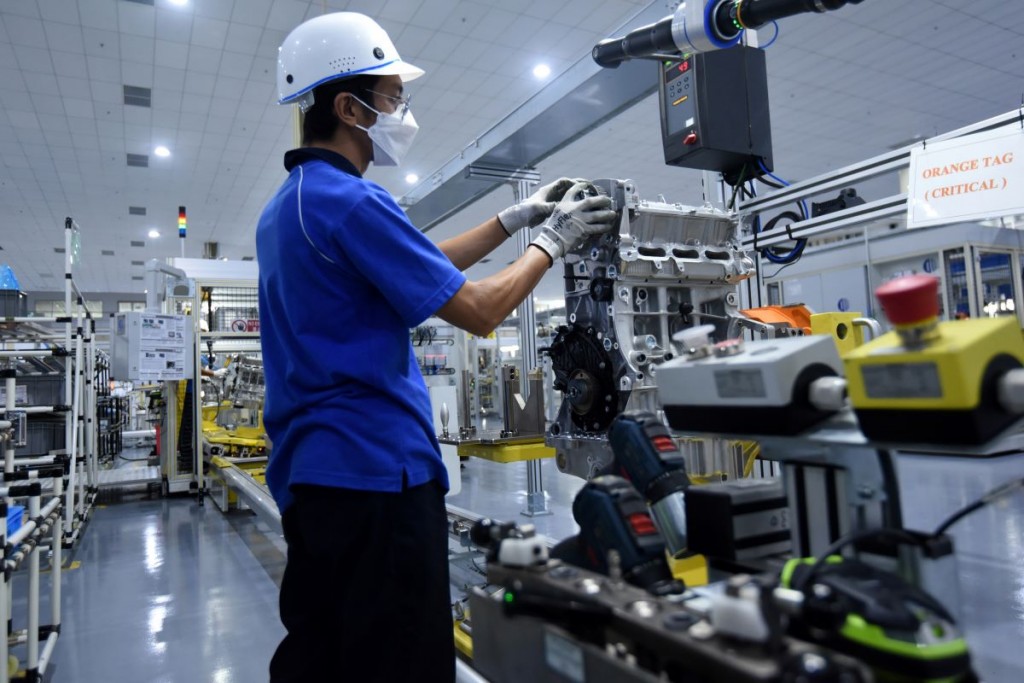
VVT sprocket installation.
Aside from powering the Proton X50 and the recently launched facelifted X70 sports utility vehicles, the award-winning engine has also been featured in multiple Geely Group automotive brands and equipped in over 750,000 vehicles sold globally.
At the unveiling of the 1.5TGDI's assembly line at Proton's Engine and Powertrain facility here today, the media was briefed on the hi-tech equipment used in its production and testing.
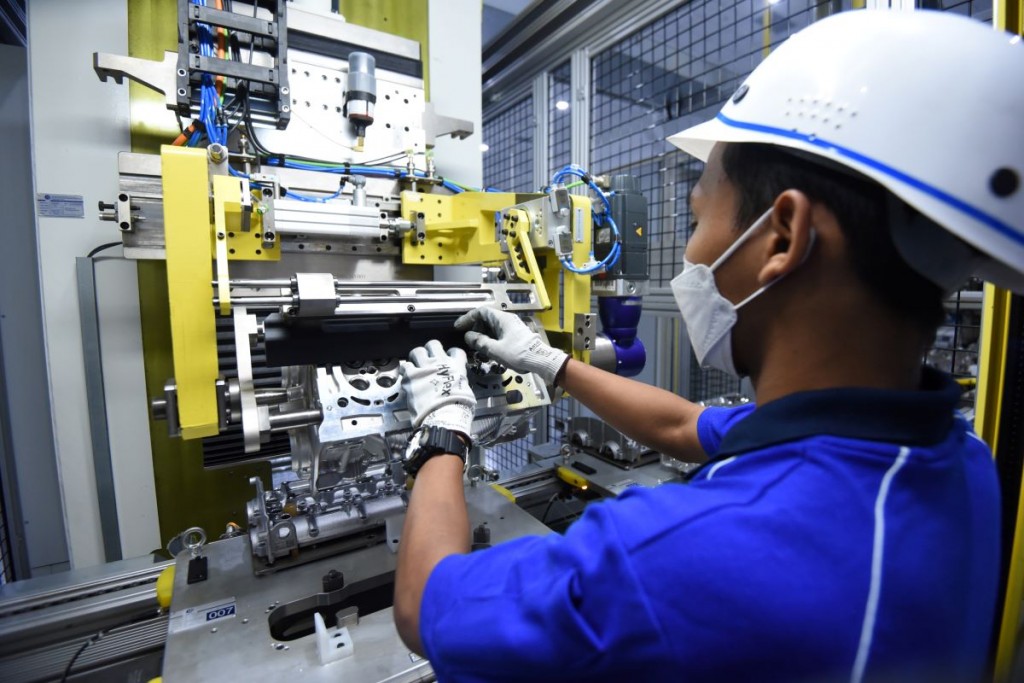
Valve assembly.
As a showcase of Geely technology sharing with Malaysian vendors and talents, the 1.5TGDI project is also part of the RM1.8bil earmarked by Proton to upgrade its facilities at Tanjung Malim.
The assembly line, which is one of the most advanced of its kind in the country, has been operational since April and is also the first outside China to produce the 1.5TGDI engine.
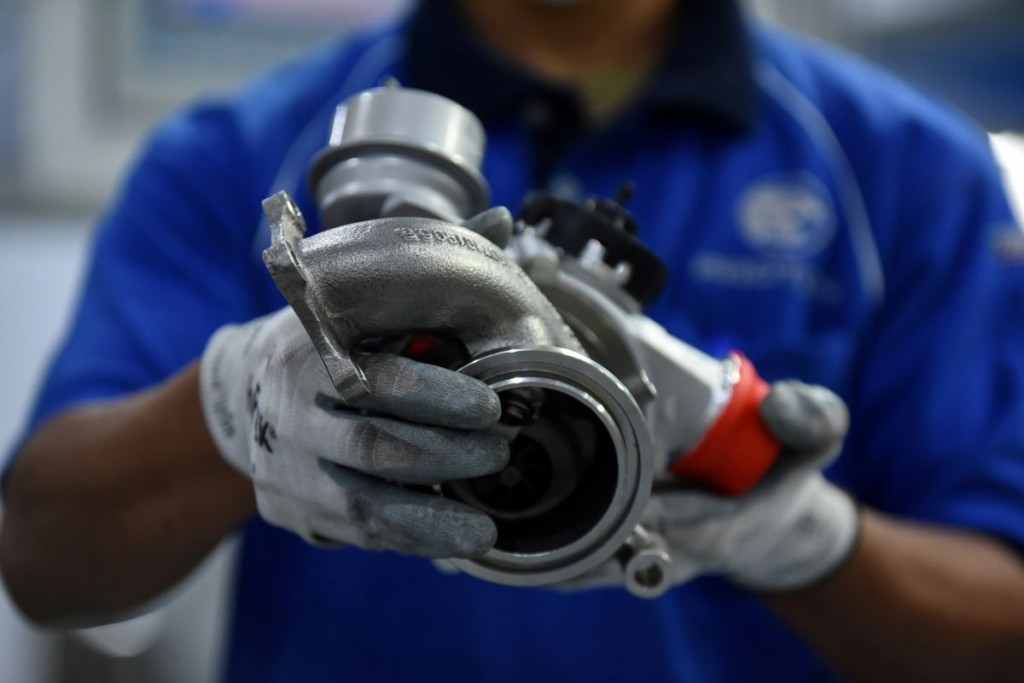
Turbocharger.
Occupying an area of 18,000sqm, the line has a current maximum capacity of making 180,000 units a year when running on three shifts.
Featuring 88 stations comprising of 17 automatic, 15 semi-automatic and 56 manual stations, the 1.5TGDI assembly line was built using an IR 4.0 approach featuring a high level of automation to boost productivity.
The line is a climate controlled clean environment which has an anti-static station to discharge static electricity and protect the high-tech electronic components used.
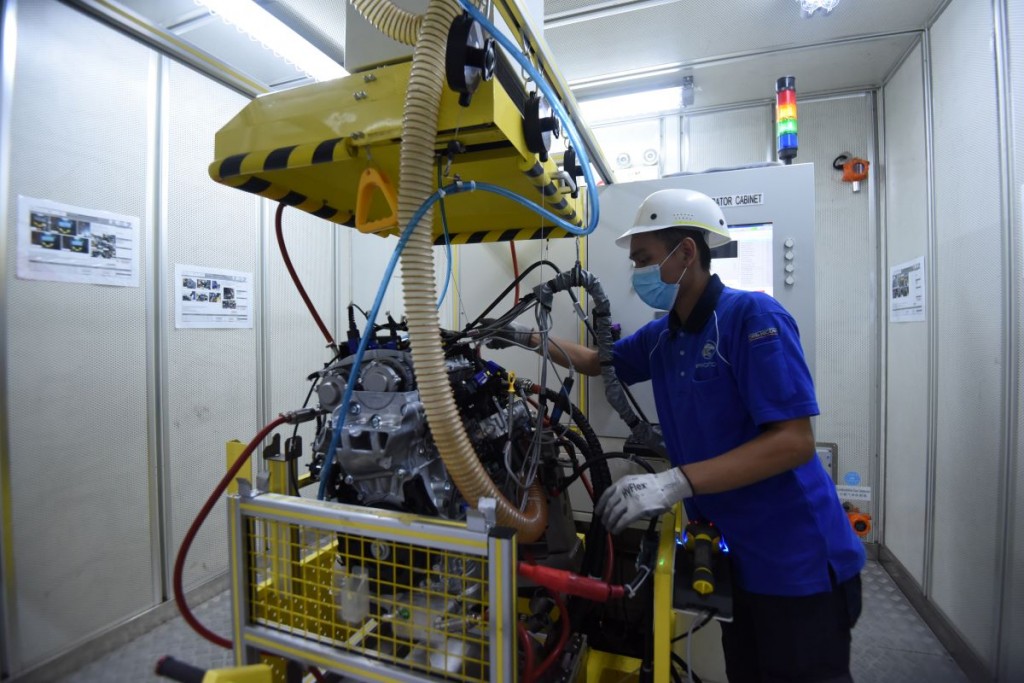
Hot testing.
It uses a conveyor system that is not only smoother but is also cleaner, more durable and less costly to operate than those using a chain system.
All workers have undergone extensive training with Geely as well as the suppliers of the machines used, which include names such as ABB, COMAU, FEV China, FEV India, WiBeda and Hangxin.
The line also deploys Internet of Things (IOT) technology such as intensive data capture and analysis tools to ensure quality meets the standards required and are maintained.
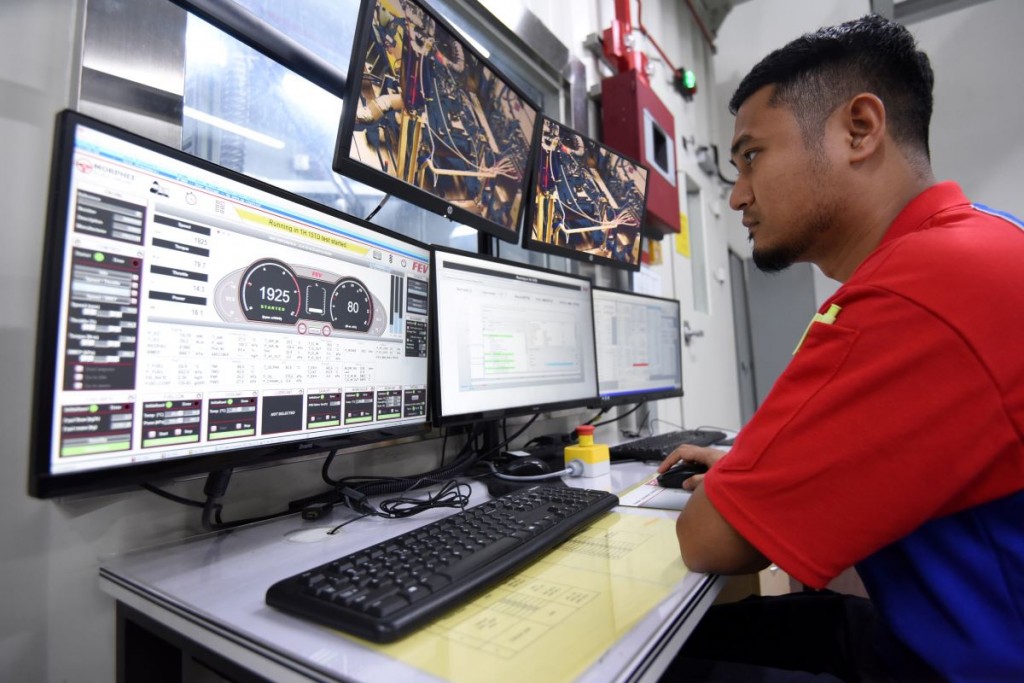
Dyno test monitoring.
Additionally, 207 Error Mistake Proofing (EMP) controls and 34 intelligent high-resolution cameras have been installed on the line to prevent process and assembly defects and reduce downtime with 100% real-time defect detection capabilities.
The 1.5TGDI engine uses parts sourced from Malaysian and regional suppliers with 72 parts supplied by 19 Malaysian and four Asean vendors.
In addition, the 1.5TGDI project also allows Proton to advance its human capital development goals with 202 workers directly employed to work there.
With an average age of just 24 years, they represent the next generation of automotive talents for the nation.
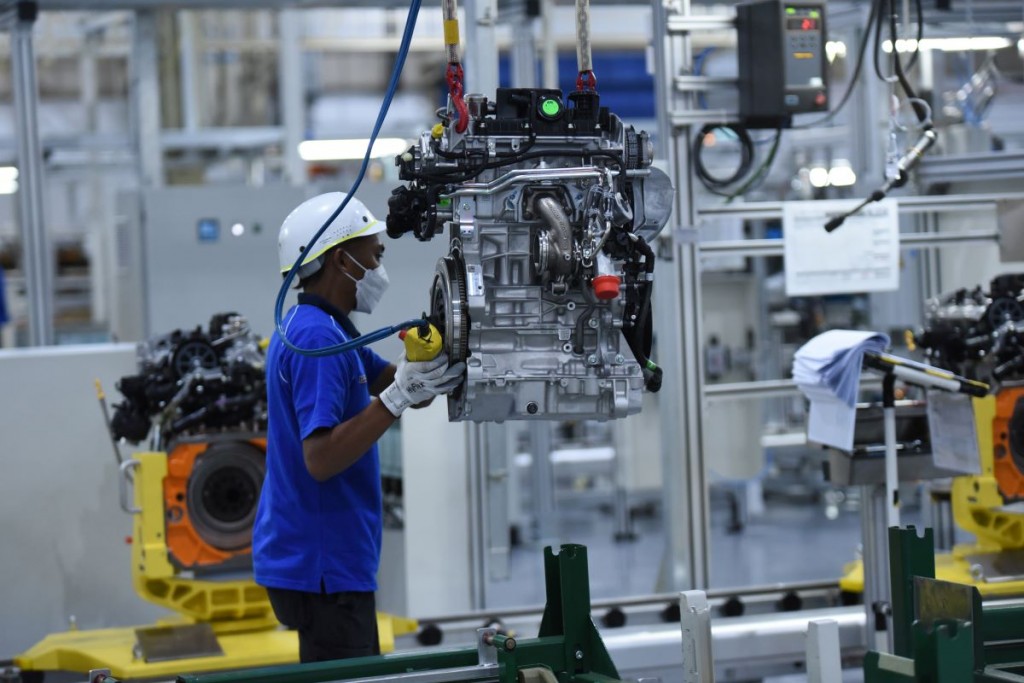
Engine line-off.
Proton Deputy Chief Executive Officer Roslan Abdullah said the company kept its promises to its stakeholders by introducing the new engine assembly line.
“When the agreement was made to partner with Geely in 2017, one of our commitments was to invest in Malaysia’s automotive industry both financially and through the introduction of new high technology components.
“Quality is the main priority at our new engine assembly line. We know we need to show Malaysians that Proton is capable of building reliable high-quality products, so we have left nothing to chance.
“Aside from the quality monitoring measures deployed on the assembly line, we also work closely with our counterparts at Geely to troubleshoot issues and share best practices in our efforts to produce a world-class engine,” said Roslan.